Click to search for other posts on webERP
In process of being updating to webERP v5.
An ERP system offers numerous advantages for manufacturing operations, primarily by centralizing data and streamlining processes. It provides real-time visibility across the entire supply chain, from raw material procurement to finished goods delivery, enabling better inventory management and reducing lead times. Automation of repetitive tasks, such as production scheduling and order processing, significantly boosts efficiency and minimizes human error. Furthermore, by integrating financial, production, and sales data, ERP facilitates more accurate forecasting and data-driven decision-making, ultimately leading to cost reductions and improved profitability. This comprehensive integration fosters enhanced collaboration among departments, ensuring everyone works with consistent information and towards shared organizational goals.
Features of using webERP for manufacturing include:
- Efficiency. Items, Vendors, Work Orders, etc. are managed within one controlled system. Fix a problem once and it’s fixed everywhere.
- Visibility. A visible, trusted, change management process and a chain of truth.
- Scalable. Readily scales with users, items, vendors and orders, and adapts as your processes change over time.
The custom inductor in the Aircraft Wireless will be used to explore basic manufacturing using webERP. Documentation will be stored in the webERP Knowledge Base (integration with WackoWiki CMS).
Goal
- Manufacture an assembly automatically issuing items on the BOM.
Manufacturing Cycle
The general manufacturing cycle in webERP is:
- Enter a Work Order to manufacture an item according to its bill of materials (BOM).
- Receive the finished manufactured items (the output from the work order) into stock. Input items listed on the bill of materials to auto-issue input items will be transacted to the work order at this time.
- Issue any additional input items used in in the manufacturing process to the work order).
- Close the work order.
The item to be manufacutured is item 100-0004, a custom electrical inductor. The inductor has been designated as as Manufactured and a Bill of Materials (BOM) has been created (for details, see Manage Parts, Suppliers and BOMs using webERP).
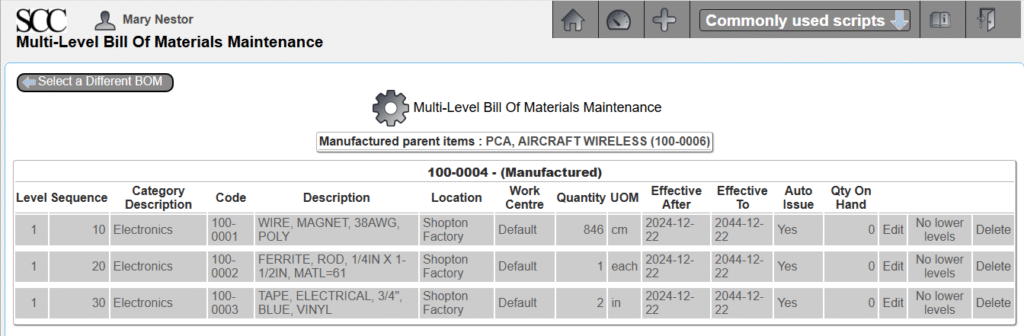
The procedure will be:
- The Manufacturing Scheduler creates work order and assigns to assembly technician.
- The Manufacturing Technician:
- Prints work order and kits required input materials from stock room.
- Initials each input item quantity as removed from stock.
- Completes finished coils.
- Initials work order showing complete and returns to scheduler.
- The Manufacturing Scheduler receives the output items into the work order, causing input items to be transferred from stock and closes the work order.
TODO add swim-lane diagrams showing manufacturing process.
TODO add examples of documentation.
User Permissions
We will login as user “mnestor” (Mary Nestor), who is assigned the Administrator security role so it won’t be necessary to understand the inner workings of the webERP role-based user security scheme before actually working with webERP. The Administrator role has all the necessary permissions for most operations (except occassionally a user with the Accountant security role will be needed for finance related operations).
In actual use however it is important each user has their own login with a password only they know. This allows correctly identifying the person performing an operation and provides tracibility. This is especially important if you will be using webERP in a regulated or controlled environment.
Default (out-of-the-box) security permissions will get you started but you should create bespoke security roles and token assignments based on the structure, staff and roles of your company.
Configuring user permissions is covered in more detail in the webERP User Permissions chapter.
Setup
TODO add setup unique to manufacturing.
Create Work Order
FOLLOWING CONTENT HAS NOT BEEN UPDATED TO webERP v5 (images and text refer to v4)
A work order essentially converts the list of raw material required to manufacture an item (the Bill of Materials, or BOM) into one or more outputs. The work order can be printed and used to kit the necessary raw materials, and also used as a traveller for the Work in Process (WIP).
- Create a new work order.
- Enter optional Reference and Remark. TODO explain why
- Search & select output item 20000001-00. Update.
- Enter Qty 10 and comment for output 20000001-00. Update.
The work order can be printed and signed as record of kitting, and also as a record of additional input items to enter before closing the work order. A printed copy of the work order often travels with the WIP as identification (also called a traveler). Labels can also be printed for later attaching to the manufactured items.
[Main Menu > Manufacturing > Transactions > Work Order Entry]
If you search for work orders you will see that the new work work is now recorded in the system.
The work order status shows demand for the raw materials needed to manufacture the inductor, which indicates they have not been issued.
You will also see that there is qty 10 of item 100-0004 on order.
Receive Output Goods
When the output items have been manufactured they are received against the work order. For simplicity I will assume the manufacturing process was flawless, with no waste and all the manufactured items meet spec (see the manufacturing and test procedure filed in the Knowledge Base). TODO correct link
Items listed on the BOM as auto-issue will issue to the work order at this time.
Process Manufactured Items Received
TODO describe procedure.
Close Work Order
Close the work order after all raw material has been issued to the work order and all manufactured items have been received against the work order. Review the work order costing,
[Main Menu > Manufacturing > Transactions > Select a Work Order > Select > Costing]
and close the work order.
Summary
This completes a basic introduction into the manufacturing process using webERP.
I am in weberp, would you teach me how to input opening balance on weberp ?
Hi Paulus, thank you for your interest. Unfortunately time constraints prevent me from providing instructions. I recommend you post your question to the WebERP forum http://www.weberp.org/forum/.