Parts&VendorsTM from Trilogy Design was the seminal PLM (Product Lifecycle Management) software in the late 90’s for small teams who needed to manage design and purchasing information. A spreadsheet approach can be perfectly adequate if you have only one BOM (Bill of Materials) and each part is sourced from only one supplier, but quickly loses effectiveness when planning or purchasing for product builds with the same part being used in multiple sub-assemblies, and it gets worse if a part is available from multiple sources. Parts&Vendors uses a database, which allows the same part to be referenced by as many assemblies as needed, or as many sources as needed.
Parts&Vendors was originally released for Windows 98SE, and provided a single point of truth for everything to do with product development (parts, BOMs, suppliers, purchasing, supporting documents, etc.) that could be accessed by anyone in the team. It even even included rudimentary inventory and build management. Parts&Vendors enabled teams to work more efficiently with more cooperation and less bureaucracy, and was affordable by the smallest businesses – only US$69/user if you didn’t need per-user login, creating purchase orders or an ECO workflow (and only slightly more if you did).
Parts&Vendors was discontinued in January 2014 when Trilogy-Design folded operations, essentially a casualty of insurmountable technical debt. Although no longer available for purchase, Parts&Vendors is the oldest software I use on a daily basis, and my gold standard for evaluating software PLM features for use by SMEs – both dedicated PLM software as well as general purpose ERP software.
Parts&Vendors Overview
Item Master Tab
Parts are accessed through the Item Master tab, and the list of parts can be sorted, filtered or searched as needed.
Item Details
Selecting a part provides detailed information on sources (vendors) as well as other useful information.
Files and URLs
Documents and web sites can be associated with a part,
making it easy to access saved documents or a web page for reference.
Although it wasn’t formal document control with a submit/approve/check-in/check-out type workflow, the simple approach was adequate for a conscientious team.
Assemblies
A part may be grouped with others in an Assembly. You can easily tell what assemblies include a particular part in PV from the part’s Used On tab.
It’s also easy to navigate from a part to a containing assembly, and back. This is also called traversing a product tree containing child parts and parent parts.
An assembly has a Parts List (aka Bill-of-Materials or BOM) that lists its child parts.
Purchasing
Parts can be easily ordered,
and an order can be left “open” to accumulate parts until it was decided to place the order, resulting in a purchase Purchase Order (PO). In some organizations the PO would be sent directly to the vendor, while in other organizations the PO would be sent internally as a “purchase request” to issue a “real” PO.
Purchasing could also be performed for a BOM, including any sub-assemblies, by selecting the top-level BOM and quantity, and generating a Purchase List,
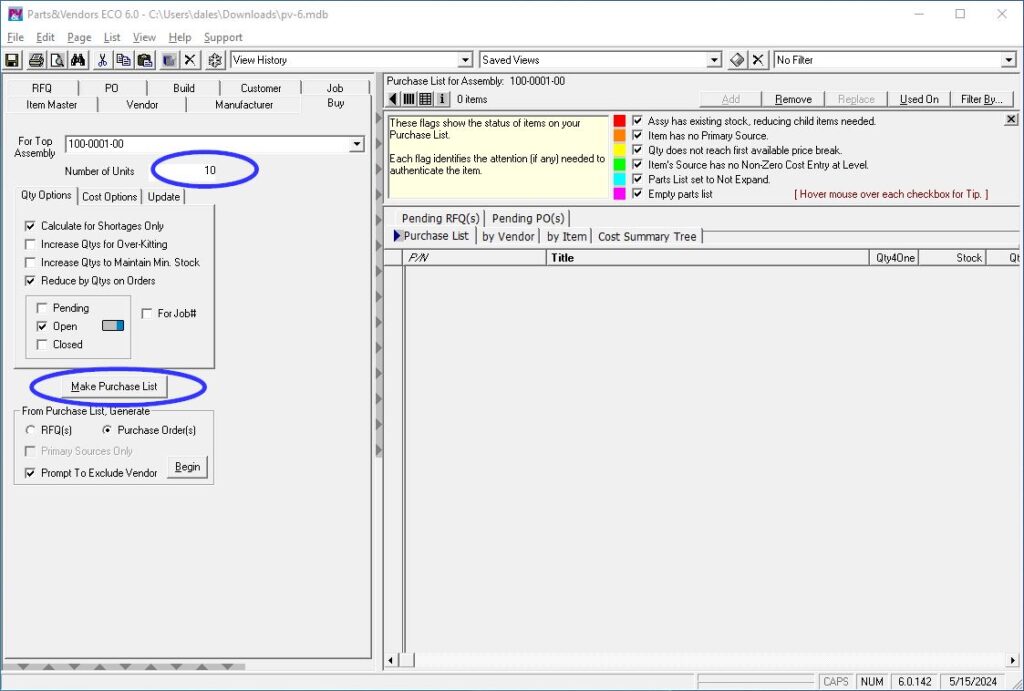
and then generating Purchase Orders from the Purchase List.
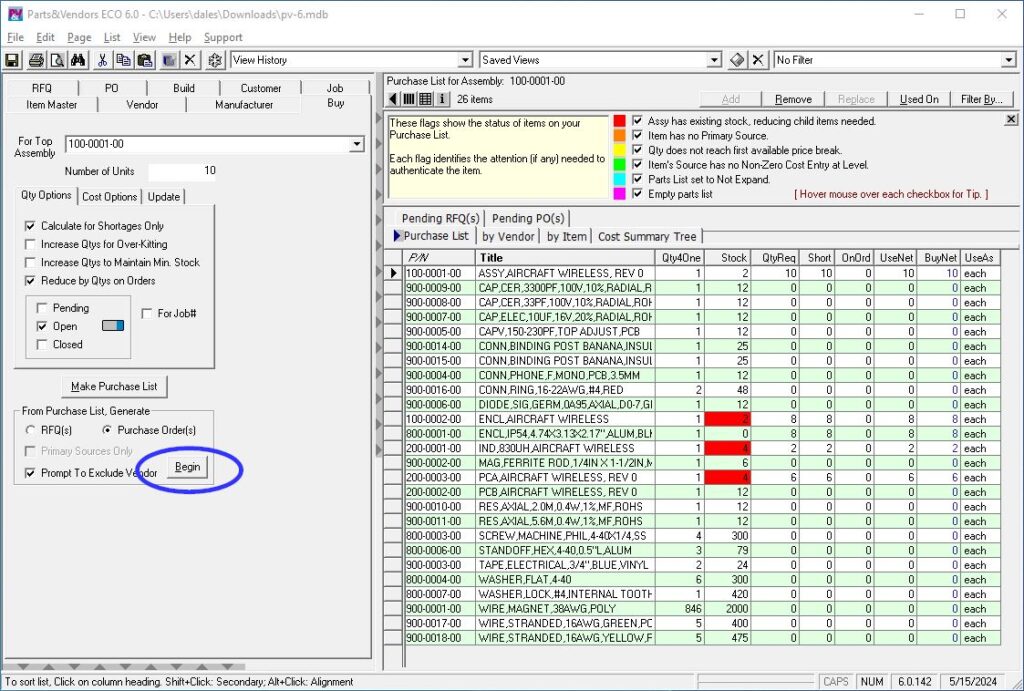
Receiving
When the ordered parts arrive, the PO is retrieved and the order item marked received,
which updates the stock on hand.
The assembly Parts List is one way to see when the parts necessary to build an assembly are in stock.
Manufacturing
Once all the child parts for an assembly are in stock, a “Kit List” is generated from the “Build” tab for manufacturing. Stock on hand can be reduced for the kitted items, and later increased for the finished assembly when completed.
Customers
PV can also manage clients and client orders, although the functionality is not integrated with stock control and closing an order does not reduce quantity on hand of the ordered items. However, the limitations were acceptable given the it was never the intent of P&V to also be a first-class POS (Point Of Sale) or CRM (Customer Relationship Management) system.
Security and User Permissions
Out-of-the-box, Parts&Vendors allowed anyone to do anything, which made setup easy and promoted user adoption. If more control was needed to prevent users from inadvertently causing trouble, user logins could be used and assigned to groups with assigned role-based permissions.
First, create a group with appropriate permissions.
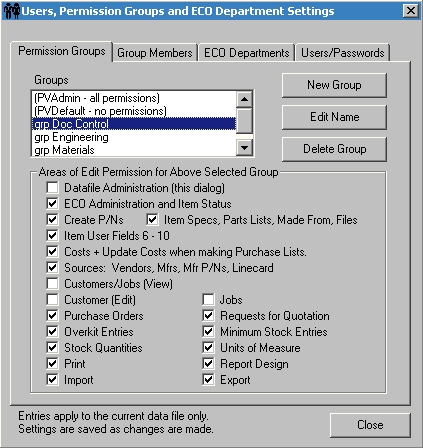
Then create a user and assign to the appropriate group.
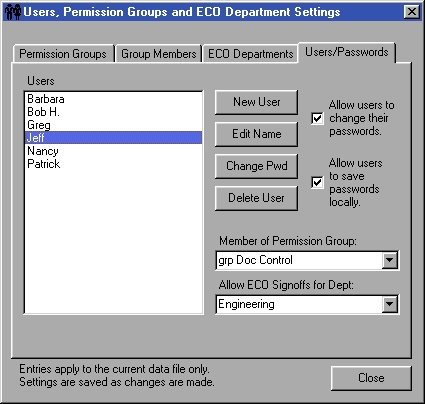
Conclusion
I hope you have enjoyed this limited look at Parts&Vendors. In my experience, it combined the features and ease of use needed for small teams to be efficient, without imposing overhead they are unable to support. The paradox of enterprise software is that you may need it once you are successful, but you won’t have the resources to use it until you are successful.
If you are using Parts&Vendors and need advise or help migrating to a new system, please contact me using the Contact form. Parts&Vendors includes built-in export capability that can be used if you are methodical, and there are also ways to access database data directly without using Microsoft AccessTM (JET database schema and user interface IDE) or if using a Unix-type operating system.